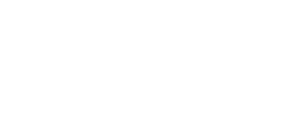
RTU32 Series
Is it a Remote Terminal Unit...
or a Programmable Logic Controller?
Leave your details and we will contact you
The RTU32 (M/N) series is the latest generation of Brodersen RTUs whose main characteristics are modularity, compactness, data collection and storage capacity, and total integration. The security aspect, combined with the ability to communicate, is a constant concern, so that it is already included at several levels, that is, instead of adding a layer of security every time a new vulnerability is found, the best solution is to have several layers of security from the conception of the product. The core components for this new RTU32 platform include ‘future-proof’ hardware with guaranteed availability of core components until 2035.
The CPU modules (MP32x) have a web server-based configuration interface for hardware configuration. Functionalities, including logic, messaging, logging, testing, etc., are configured through the Worksuite software. In addition, the integrated web server generates HTML5 pages for viewing process screens that can replace local HMIs.
In addition to all the capacity for data collection, storage, processing and process control, the features and cloud integration functionalities of the RTU32 make them an excellent solution for the digitalization and insertion of plants and processes in the Industry 4.0 journey.
RTU32M
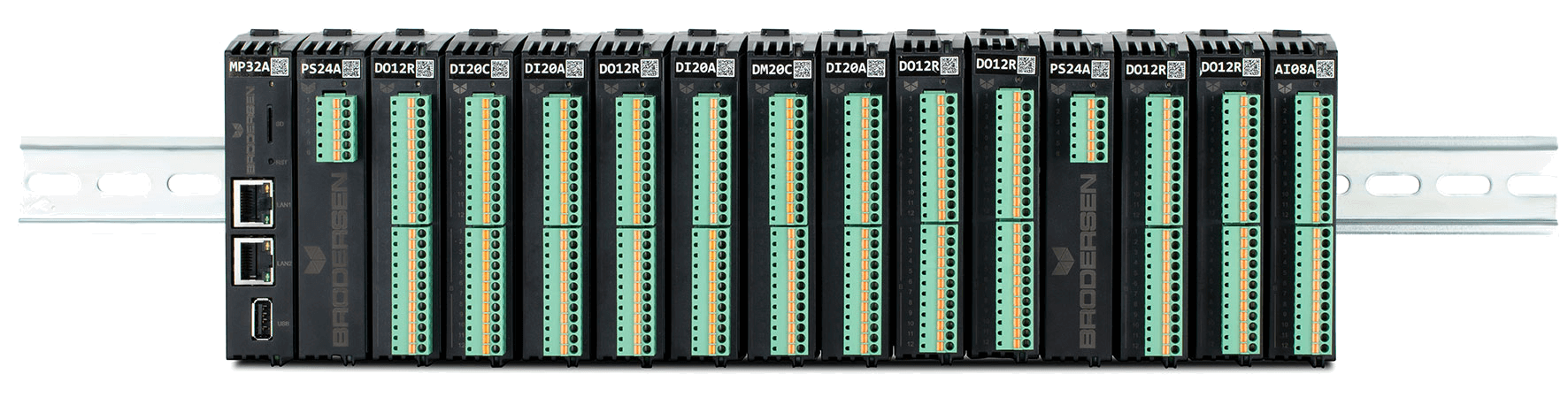
RTU32M is a compact, modular, and totally innovative control and data acquisition system with features that allow it to be used both in process automation solutions and in remote monitoring and/or data acquisition. Its compact, modular, redundant, and flexible physical structure provides great space savings in the cabinets, without neglecting scalability, with the possibility of adding local, remote or distributed I/O modules, including through fiber-optic interface modules.
With a 32-bit architecture, each RTU32M consists of a CPU module, power module in various options, mix of smart input and output modules, and system modules, which can be three-phase IEDs, 4G/3G/EDGE/GPRS/IoT modem, fiber-optic modules, and modules with additional LAN and serial communication ports.
The RTU32M supports a variety of standard and open protocols, such as Modbus, IEC60870, IEC61850, DNP3, Ethernet/IP, MQTT, OPC UA, SNMP etc. In the topology, the event-based binding protocol (binding) is a fast and reliable way to distribute event data across any CPU or remote on the network.
Special attention is paid to operational safety with redundancy at all levels. CPU and power supply redundancy in the same rack, power supply and CPU redundancy in different racks addressing the same I/O, or full redundancy, CPU, power supply and I/O in different racks are the options available, depending on the degree of security required. Ethernet network redundancy is also available through the HSR/PRP driver.
CPU and power supply redundancy in the same rack
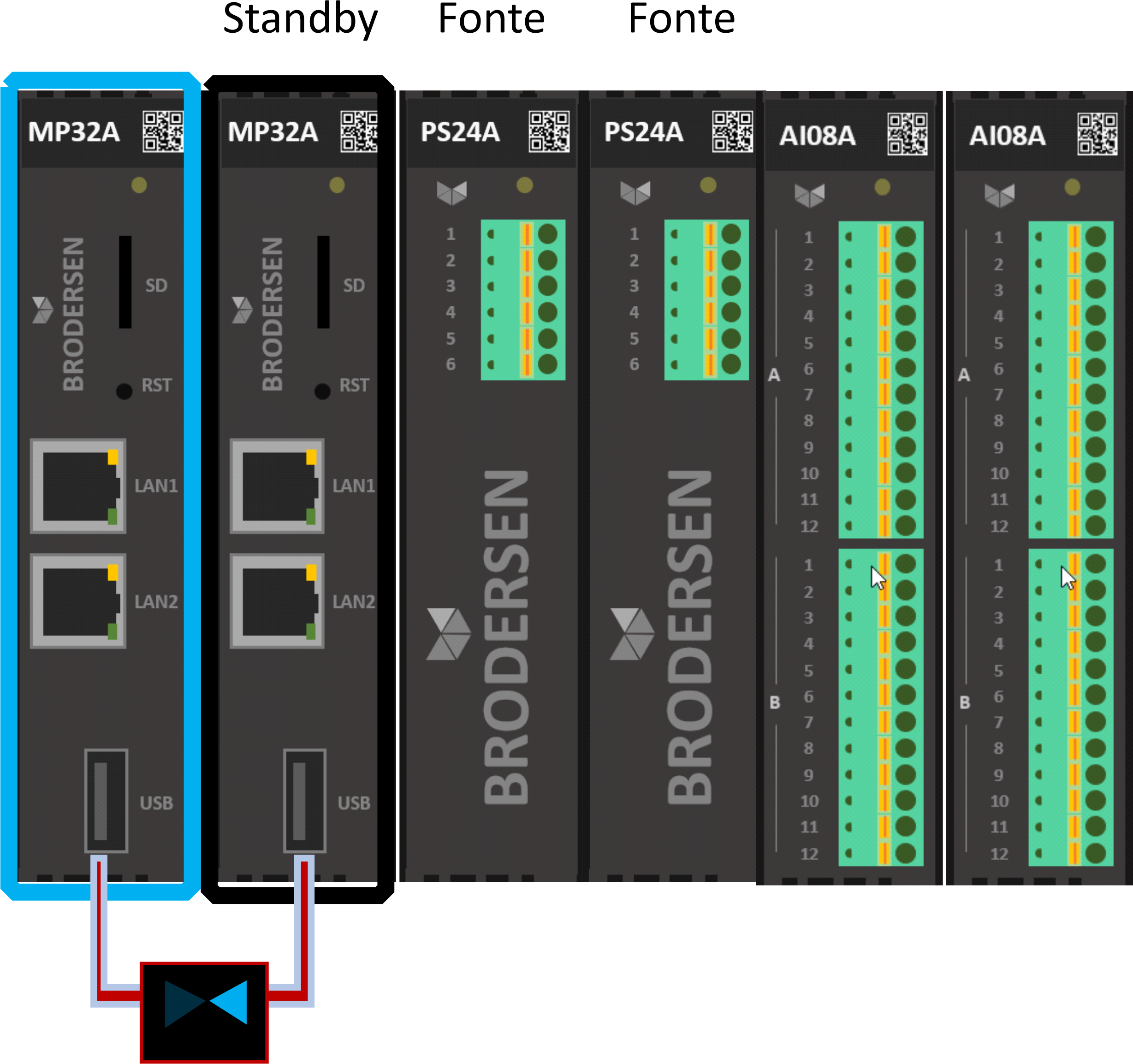
The “classic” redundant solution. This redundancy does not provide the highest degree of protection against CPU and/or power supply failures, but it is a well-known layout, as most PLCs/RTUs only offer this type of redundancy. The data is mirrored via the bus and via the REDLINK connection. You only need to program one CPU module – the program is automatically mirrored to the redundant CPU. Its implementation is easy, since in a non-redundant system it is only necessary to install the second CPU and connect the REDLINK cable. The system does the rest on its own.
CPU power supply and communication redundancy, sharing I/O
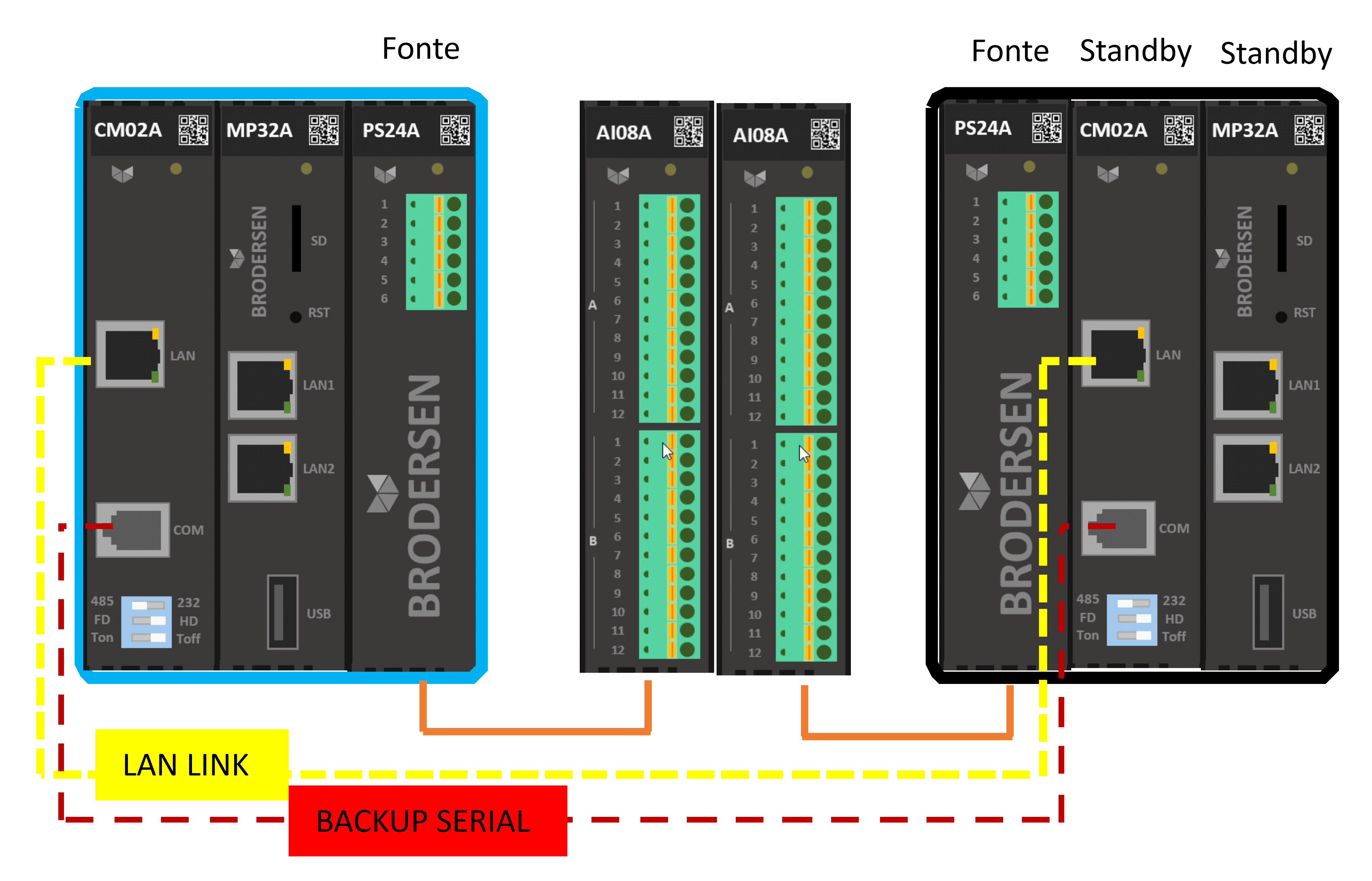
The stratification of the system provides greater availability precisely because of the physical separation. Problems that eventually occur on a bus do not affect the redundant system bus. The CPUs and the shared I/Os can be in separate cabinets. In this type of redundant configuration, the CPUs scan the I/Os, both on the operating CPU and on the stand-by CPU. You only need to program one CPU module – the program is automatically mirrored to the redundant CPU. It is also easy to implement, since in a non-redundant system it is enough to install the redundant rack. The system does the rest on its own.
Separate CPU, power supply, communication, and rack I/O redundancy
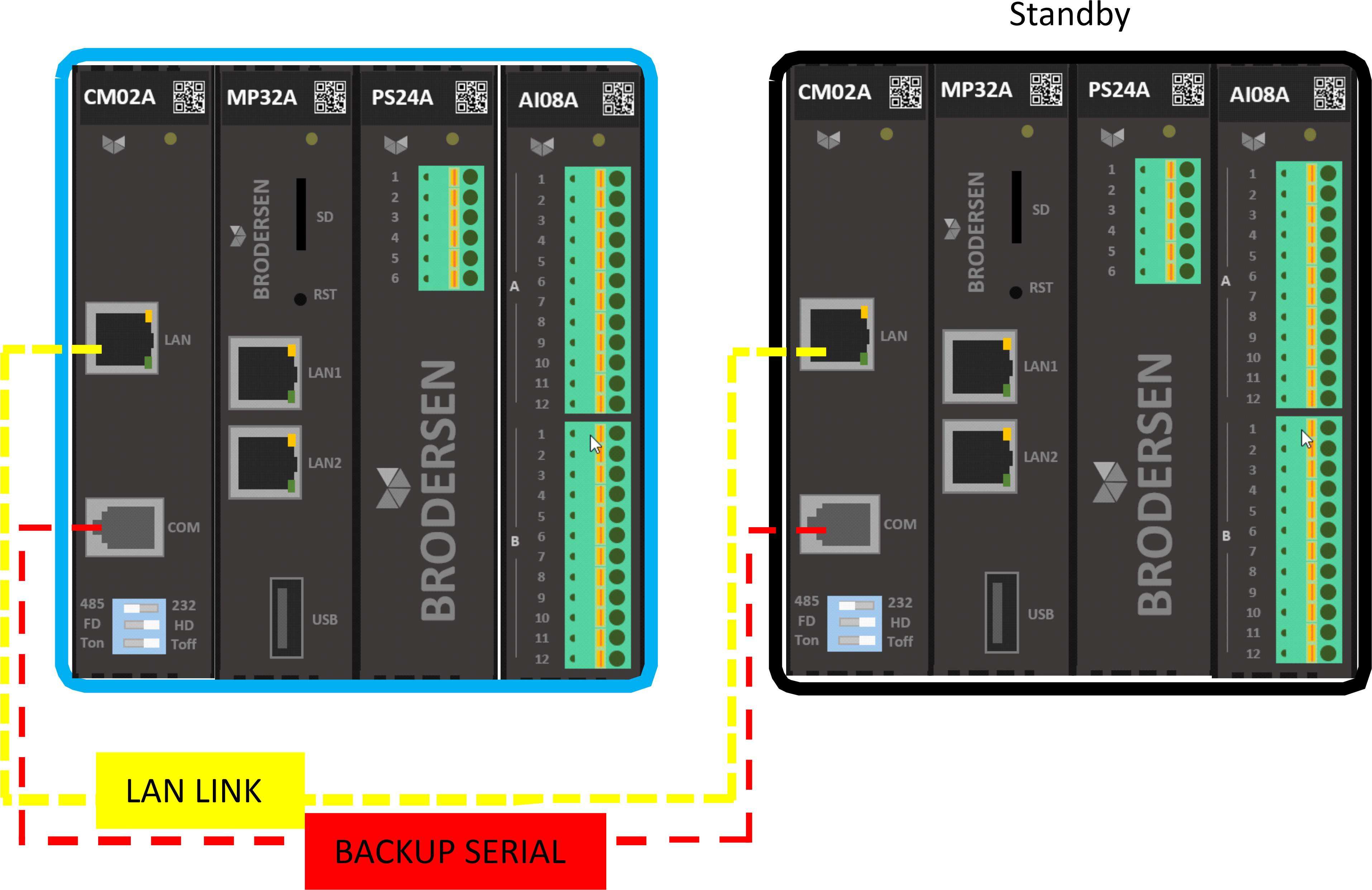
Full redundancy – Duplication of all hardware provides a high degree of redundancy and reliability. The two CPUs are connected by a LAN cable and a serial cable. The LAN cable replicates the data, and the serial cable is an active link in the event of a LAN cable failure. You only need to program one CPU module – the program is automatically mirrored to the redundant CPU. The two systems can be in different locations to minimize the risk of power supply problems, fire, lightning strikes, etc. It is also easy to implement, since in a non-redundant system it is enough to install the redundant rack. The system does the rest on its own.
RTU32M - Main features:
- Fully modular and compact
- Multiple CPU models with multiple communication ports
- Fully flexible topologies
- 3 types of redundancy
- Dual VPN
- Firewall
- LDAP User Authentication
- PPP/link serial
- HSR/PRP network redundancy
- Encrypted data storage
- Up to 60 I/O modules on each CPU
- HTML5 operational pages via embedded webserver
- 200/528/900/2GHz processors
- RAM 128/256 MB and 4GB
- NAND/NVRAM 128MB+128MB
- Three-phase IED modules
- FO modules (single/multi-mode SC, multi-mode RT)
- 4G LTE IoT Modem Module
- Automatic configuration of I/O modules
- Native SOE
- Various standardized communication protocols (Modbus, IEC 61850, IEC 60870-5-101/103/104, DNP3, OPCUA, MQTT, Ethernet/IP, SNMP etc)
- Upgrade of features and functionalities, such as inclusion of drivers, CPU speed, RAM and amount of I/O, through software, without changing the CPU.
See who uses our RTUs

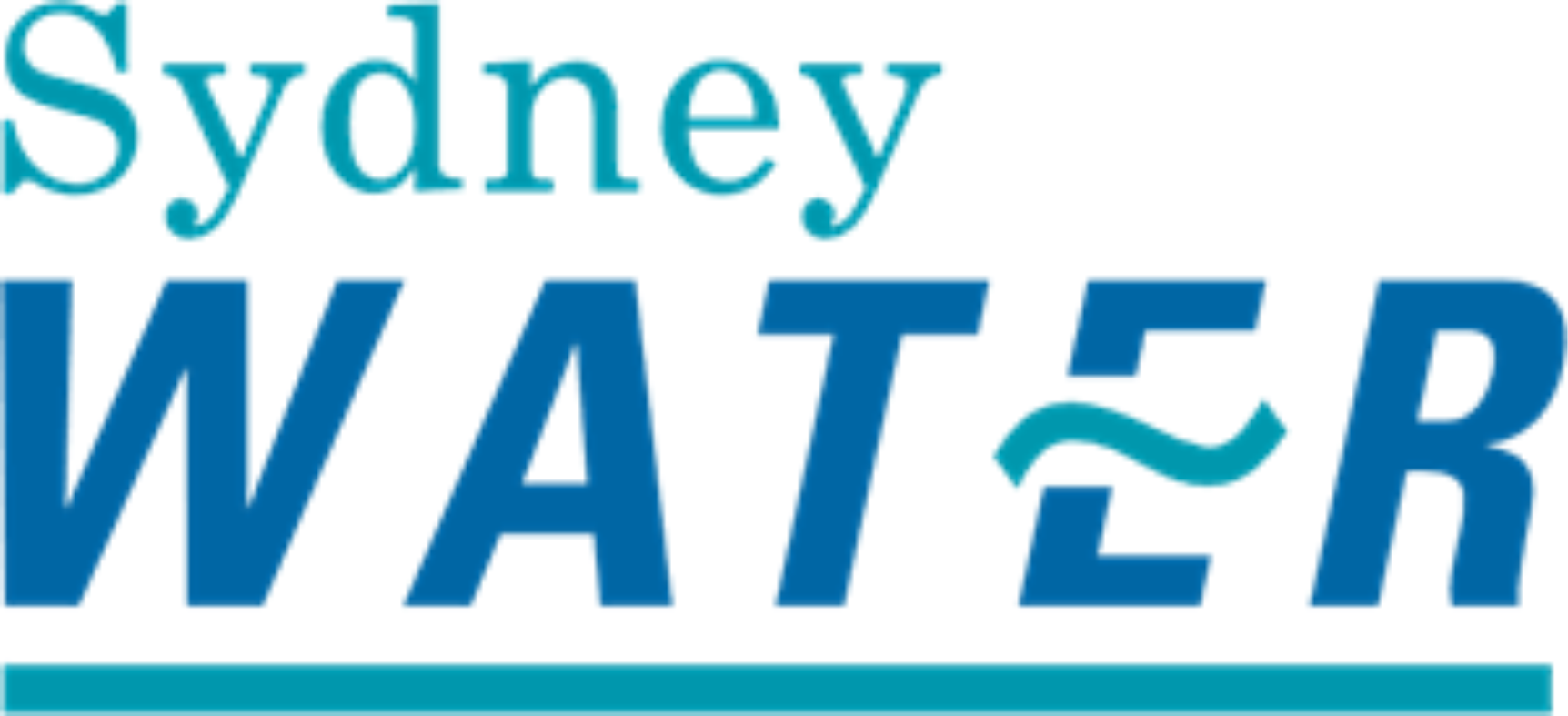

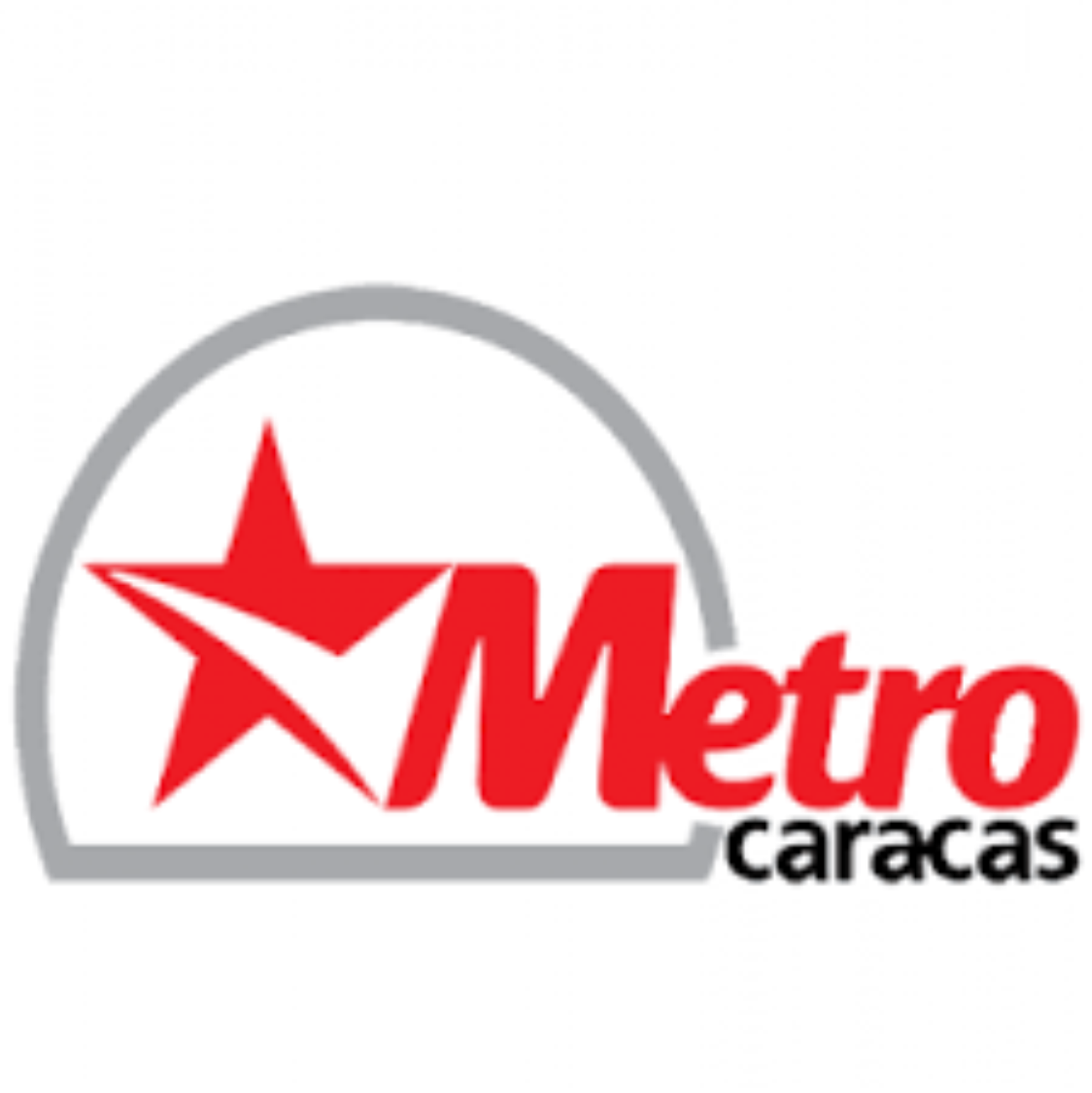
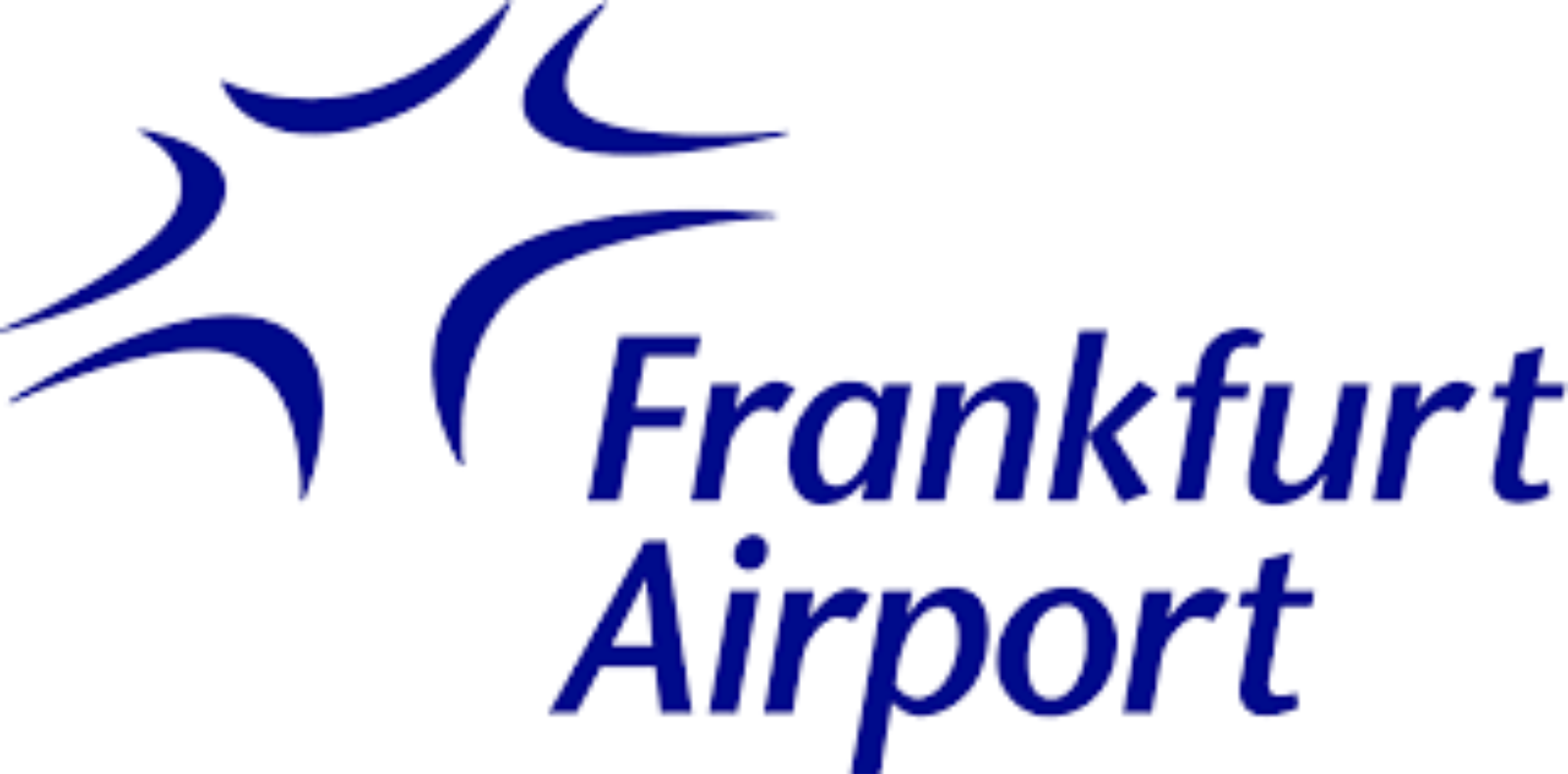
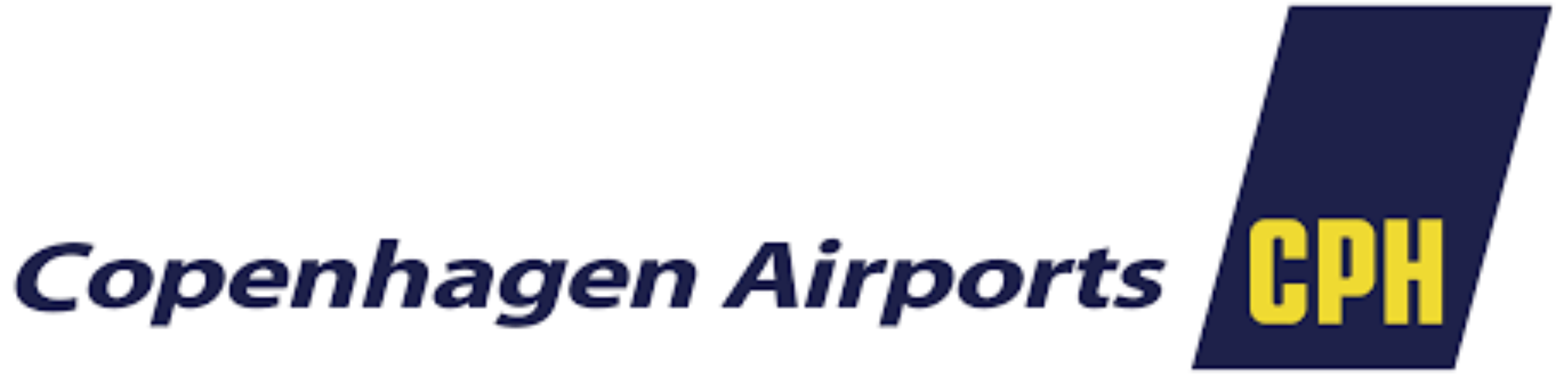
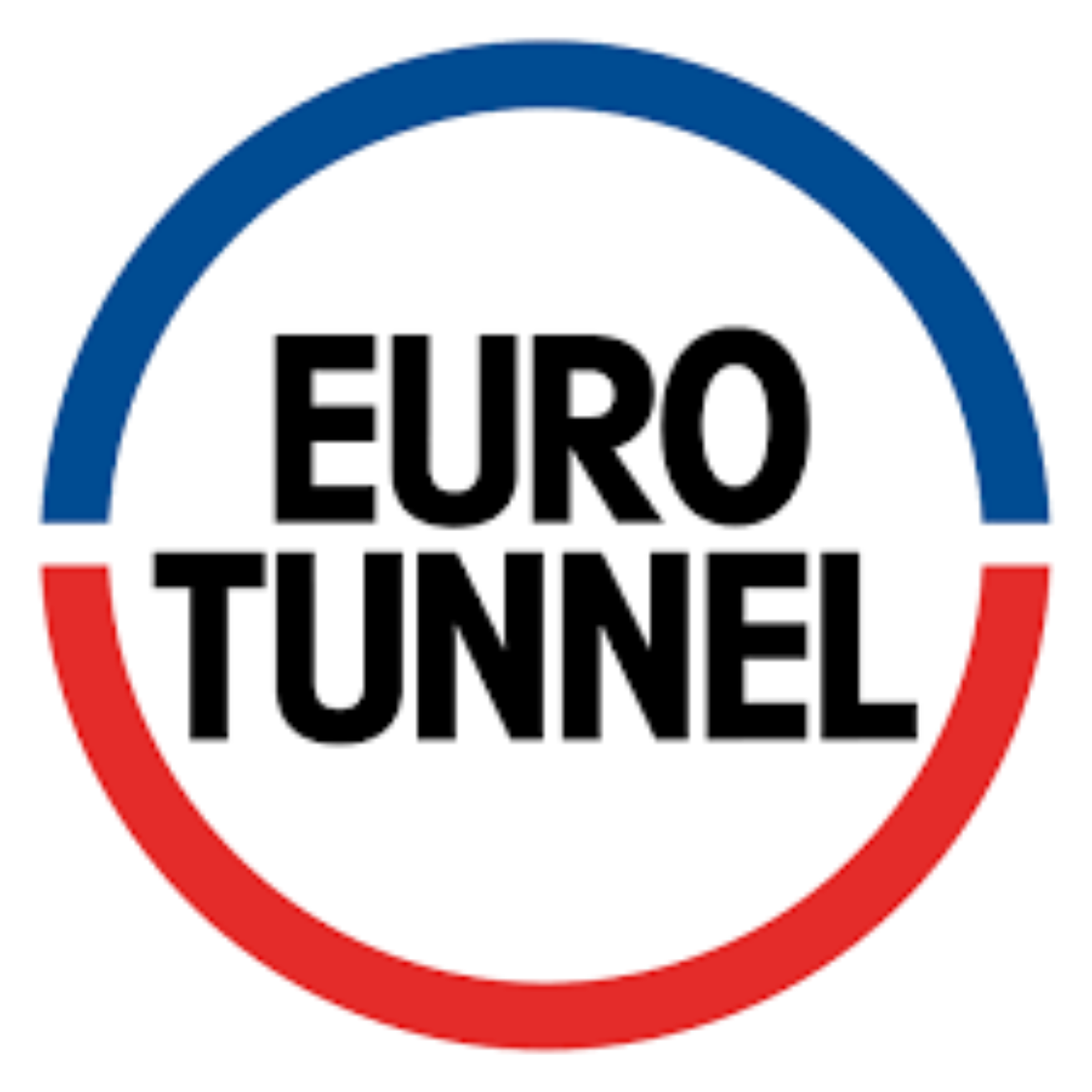
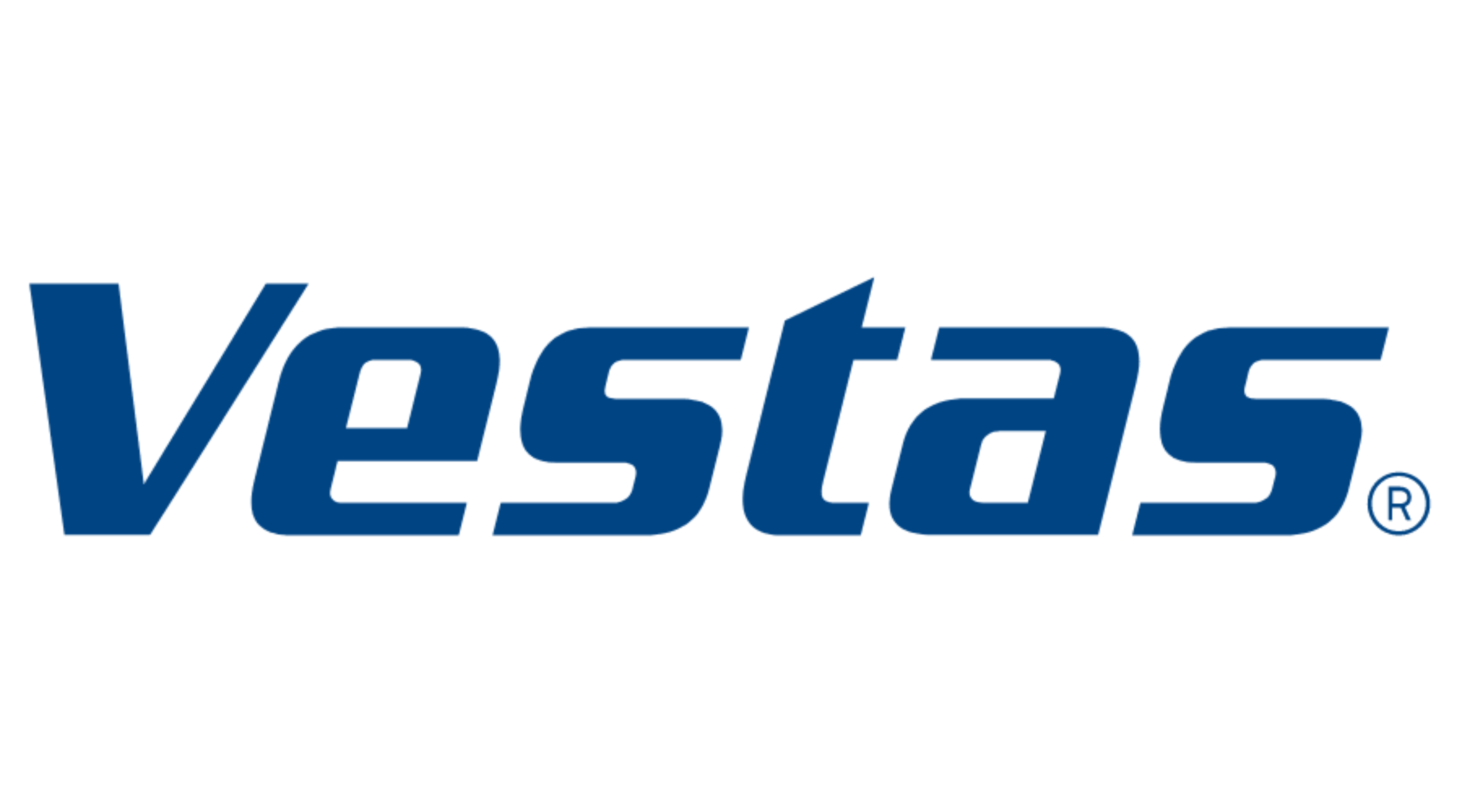

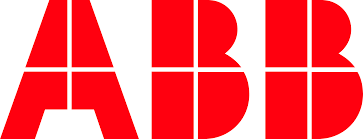
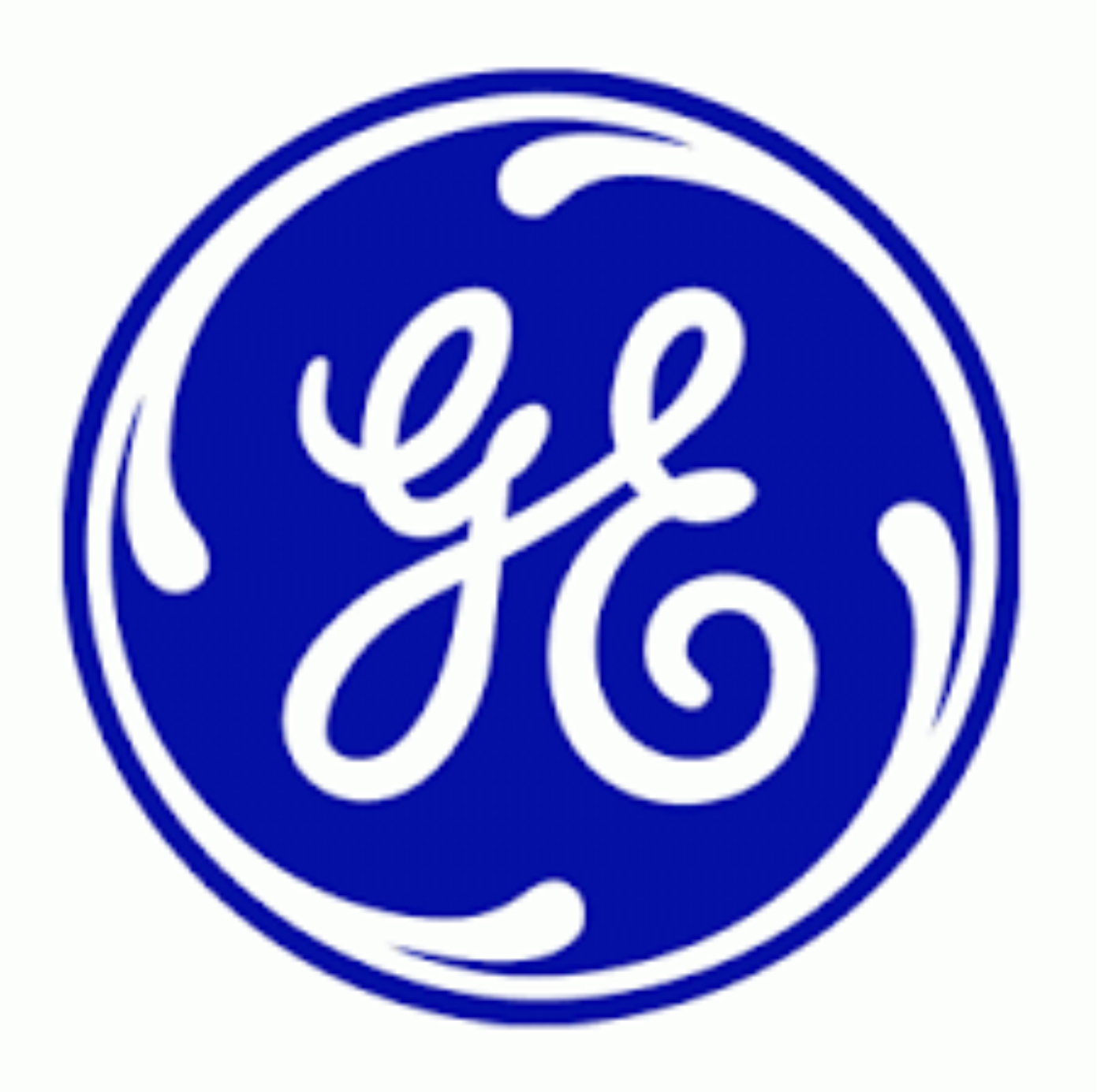
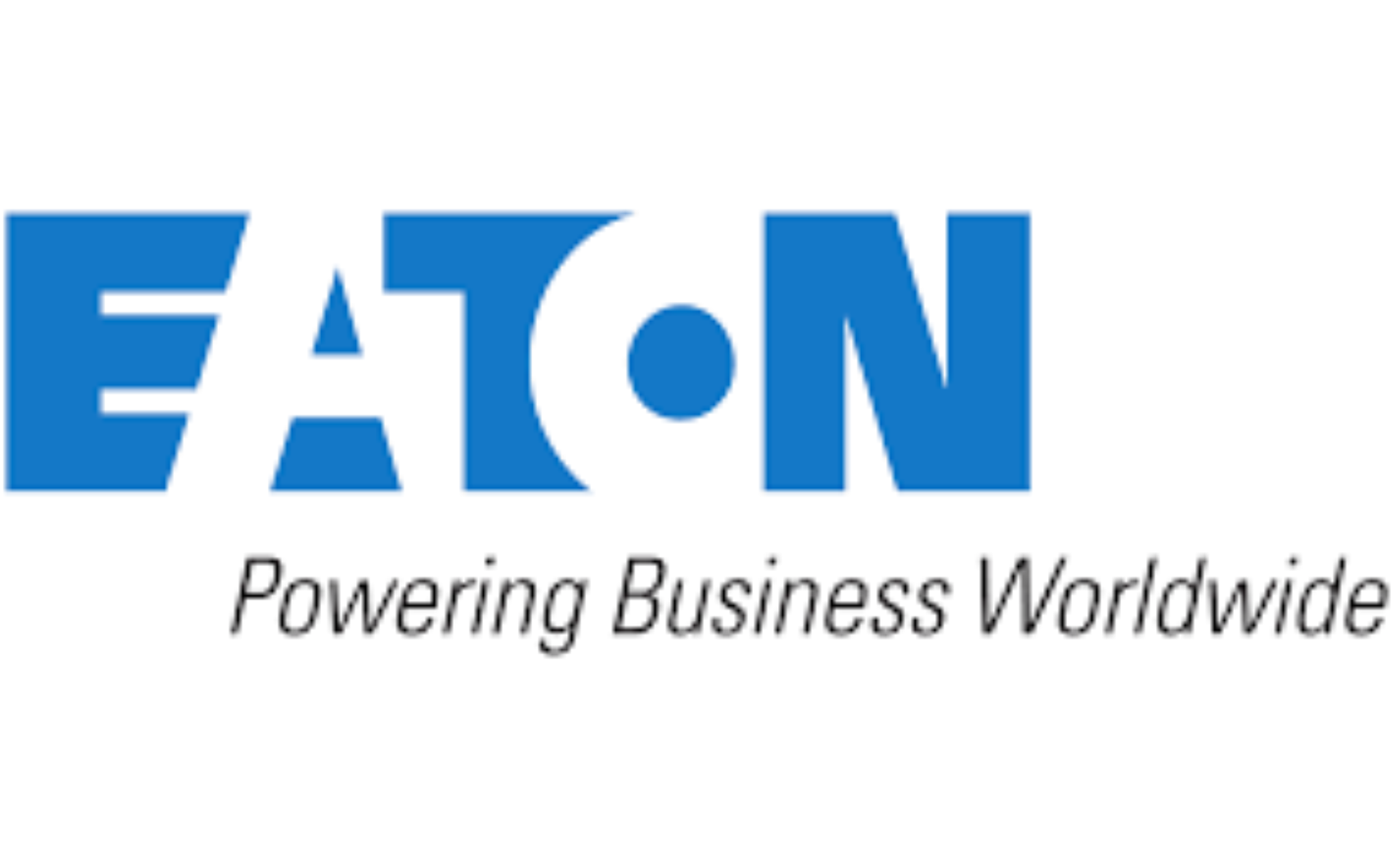

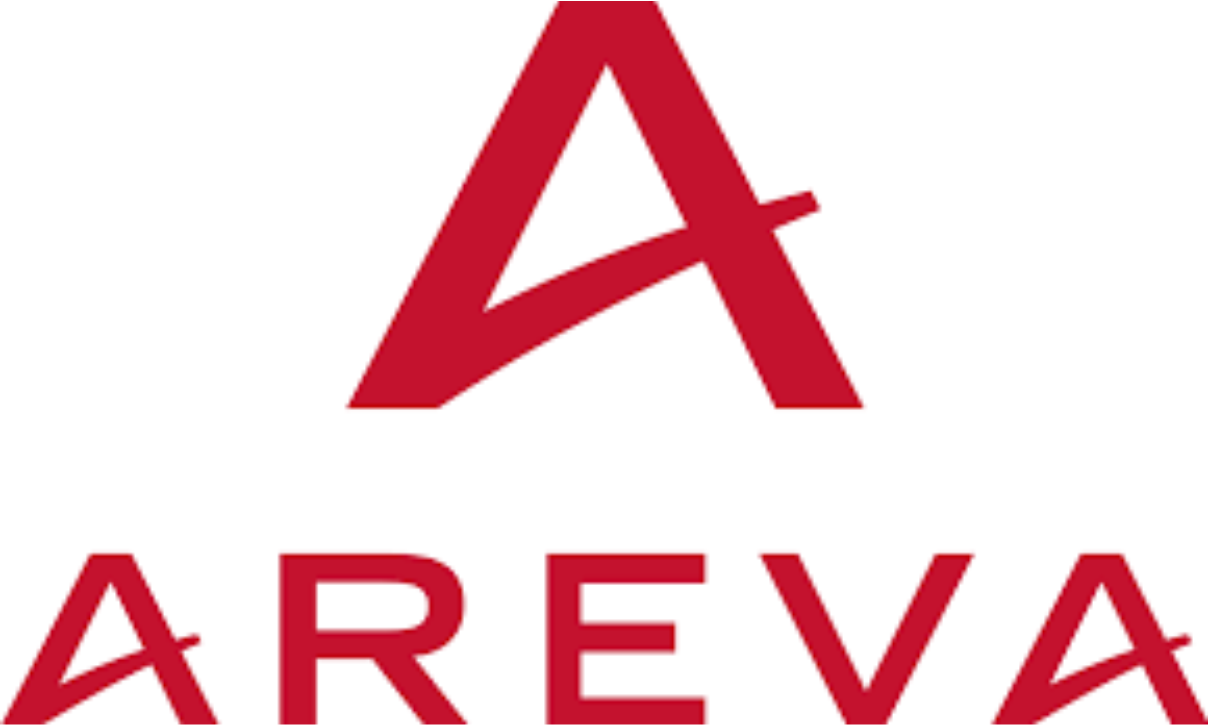
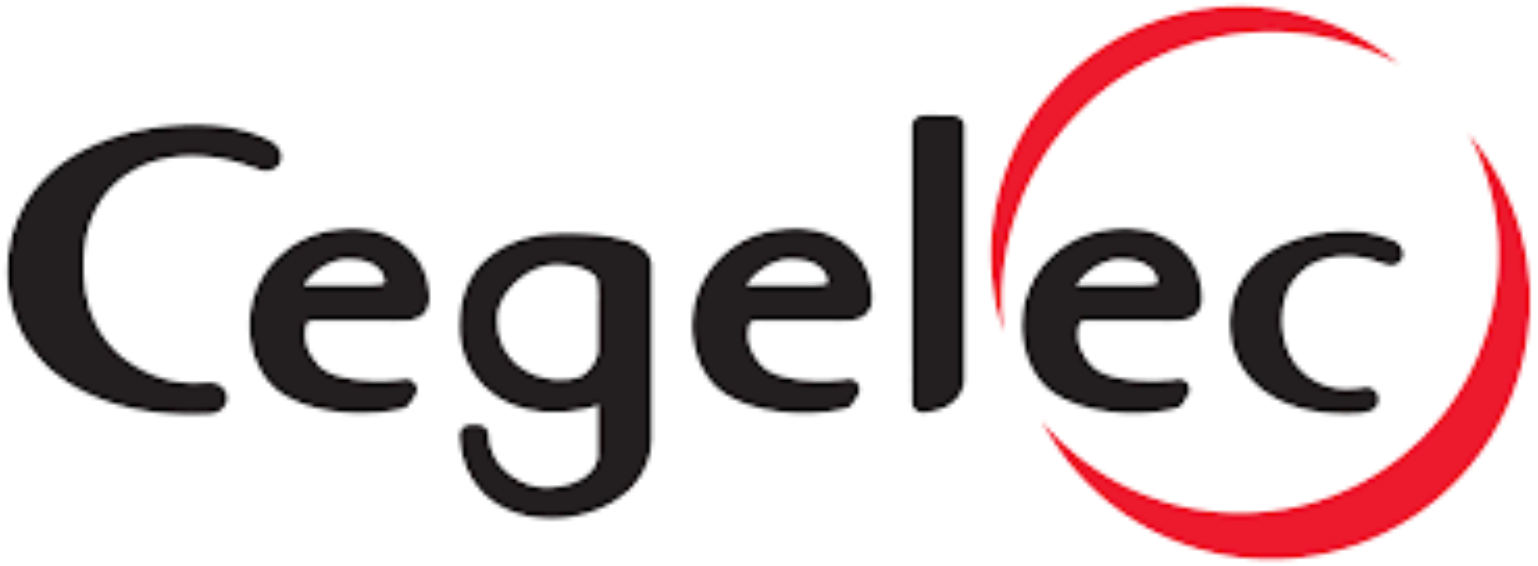
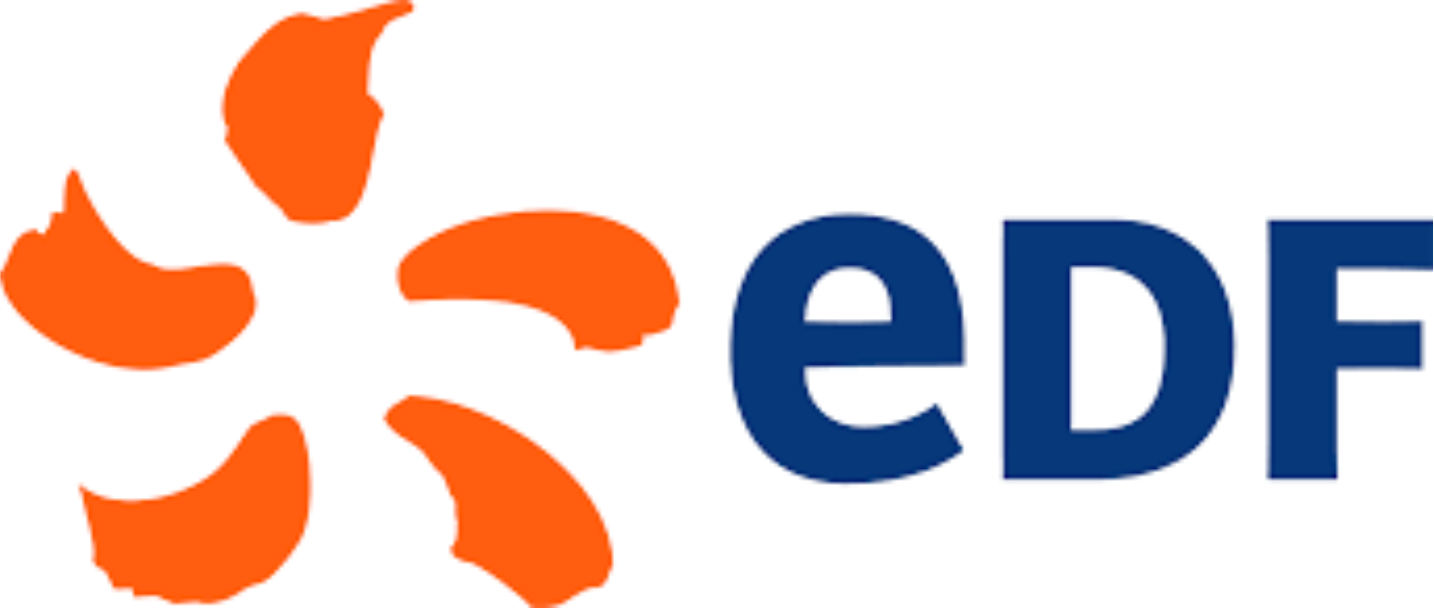
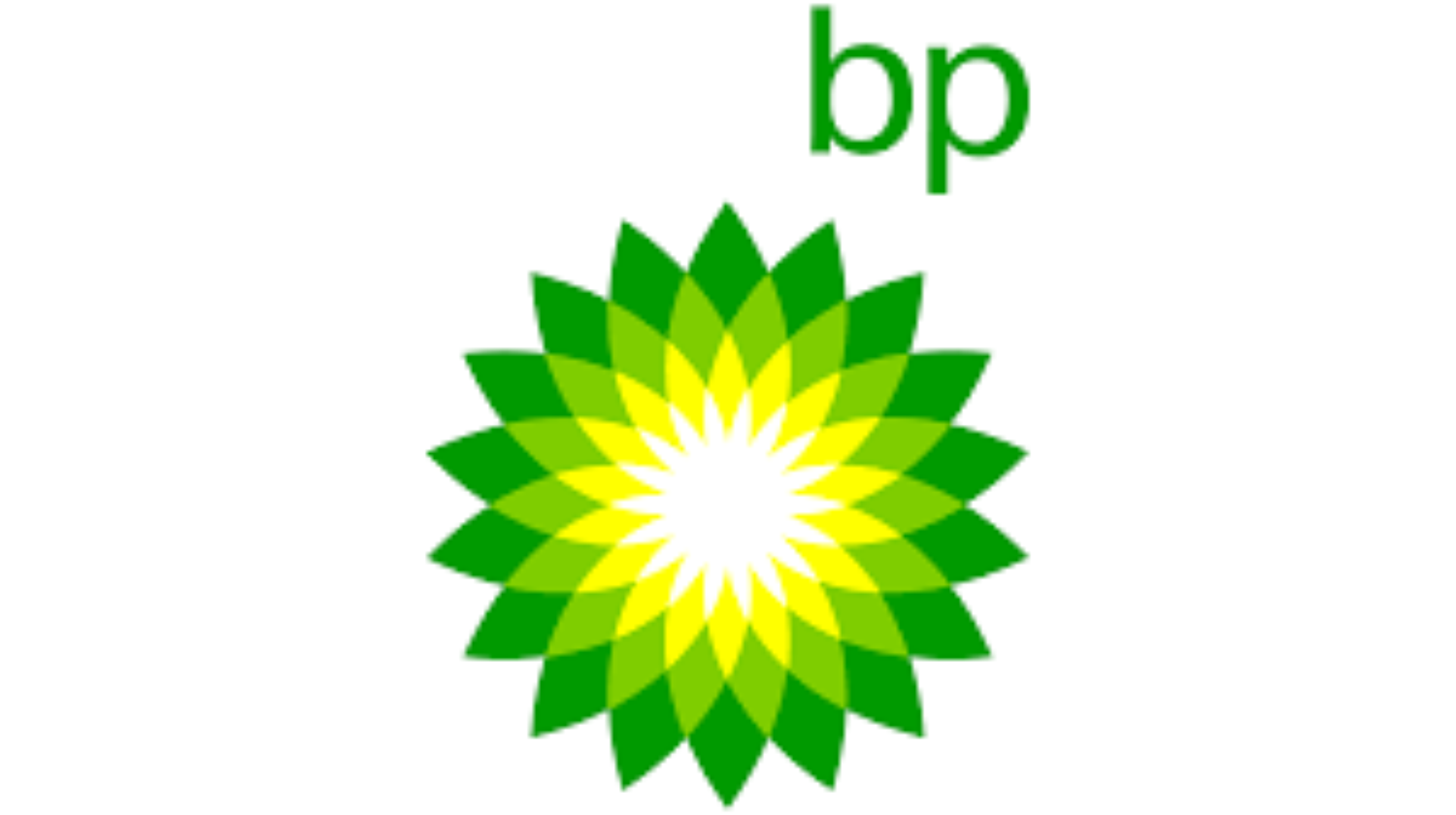
RTU32N
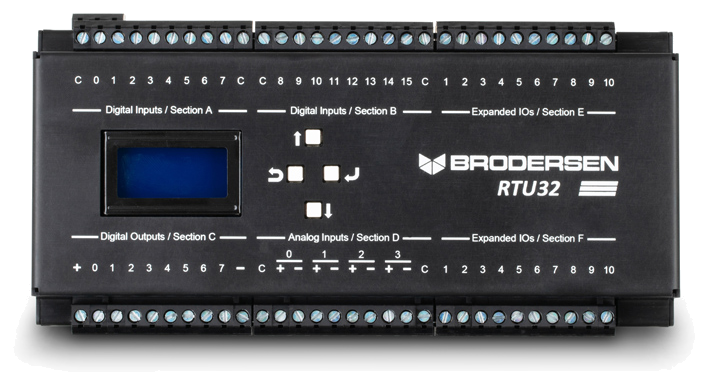
The RTU32N series is the integrated version of the Brodersen family of controllers/RTUs. With a 32-bit architecture, it offers both PLC functionalities with programming in accordance with IEC 61131-3 and data storage and communication functionalities, which makes it possible to use it not only as an RTU, but also as a programmable controller for advanced industrial applications.
Physical communication interfaces include 2x 10/100 Mbps LAN, 4x RS-232/422/485 ports, and 2x USB 2.0. The RTU32N also offers support for communication devices such as radios, GSM/GPRS/3G/4G etc., making it the perfect solution for data acquisition in remote locations without a physical communication network.
The RTU32N supports a variety of standard and open protocols, such as Modbus, IEC60870, IEC61850, DNP3, Ethernet/IP, MQTT, OPC UA, SNMP etc. Like the RTU32M, the event-based binding protocol (binding) is a fast and reliable way to distribute event data across any CPU or remote on the network.
The CPU module (UCN-xxx) has a web server-based configuration interface for hardware configuration. Functionalities, including logic, messaging, logging, testing, etc., are configured through the Worksuite software.
In three versions that differ by the amount of I/Os, (without I/O, 28 I/Os and 42 I/Os), it also has versions for 10-30 Vdc and 30-60 Vdc power, in addition to the option of external UPS power (UCS-CHRxxx). Despite being a version with integrated I/O, the RTU32N can use all the modules of the LB2 intelligent I/O system for eventual expansion.
Main features:
- Dual VPN
- Firewall
- LDAP User Authentication
- PPP/link serial
- HSR/PRP network redundancy
- Encrypted data storage
- Up to 60 I/O modules on each CPU
- HTML5 operational pages via embedded webserver
- Uses all LB2 I/O modules
- Automatic configuration of I/O modules
- Native SOE
- Various standardized communication protocols (Modbus, IEC 61850, IEC 60870-5-101/103/104, DNP3, OPCUA, MQTT, Ethernet/IP, SNMP etc)
- Upgrade of features, such as inclusion of drivers, CPU speed, RAM and amount of I/O, via software, without changing the CPU
LB2 Intelligent I/O Module System
The LB2 Intelligent I/O Module System is designed to meet the RTU32M and RTU32N families of PLCs/RTUs and their redundant architectures. There are digital and analog input and output modules, relay modules, mixed modules, with various I/O densities, as well as IED modules, fiber-optic interface, modem and modules for expansion of communication ports that give the system robustness, scalability and reliability. They are divided into two parts, the backplane, which contains the bus, and the I/O and logic board. All LB2 I/O modules have 2 kV isolation and can be hot-swapped, in addition to having a 200 Mhz processor for I/O processing, filters, SOE, which is native to all I/O points, clock and logic of the module in general.
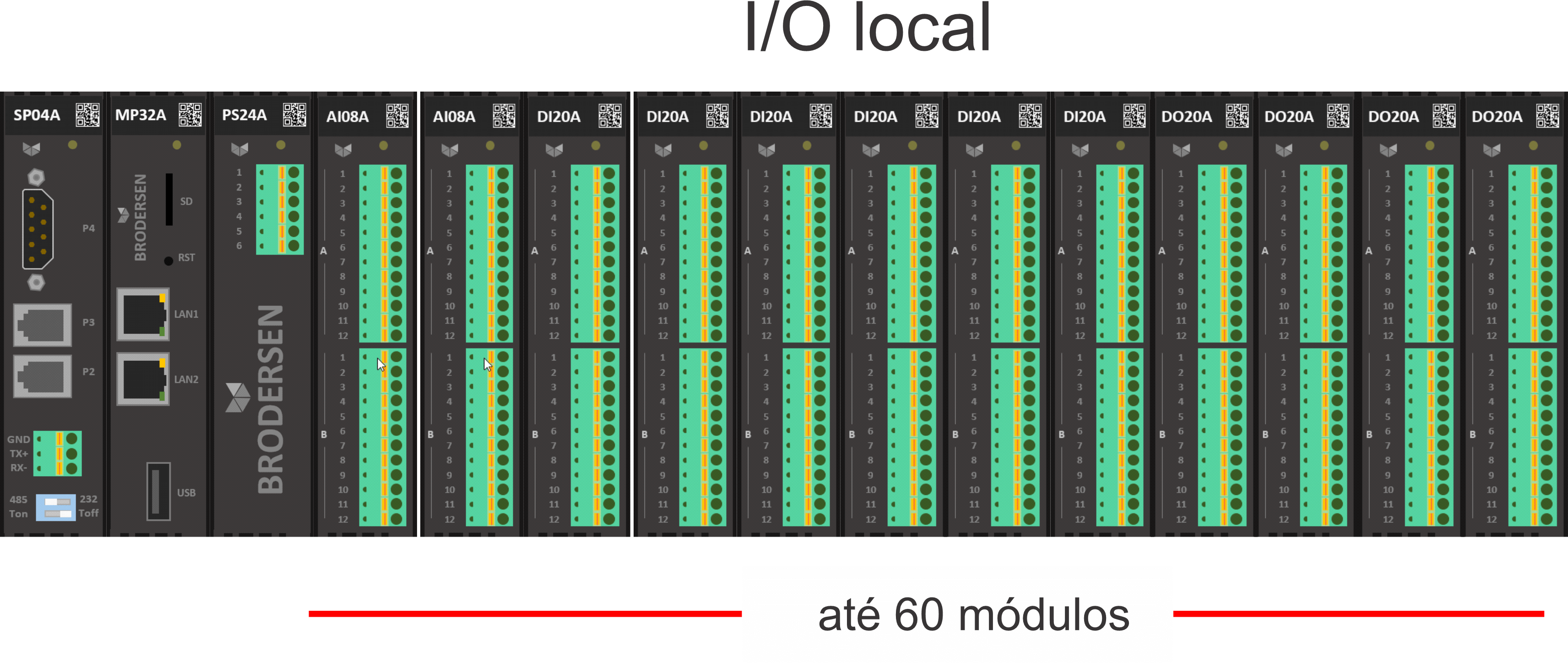
The maximum amount per CPU is 60 modules, and if more modules are needed, a CPU can be added.
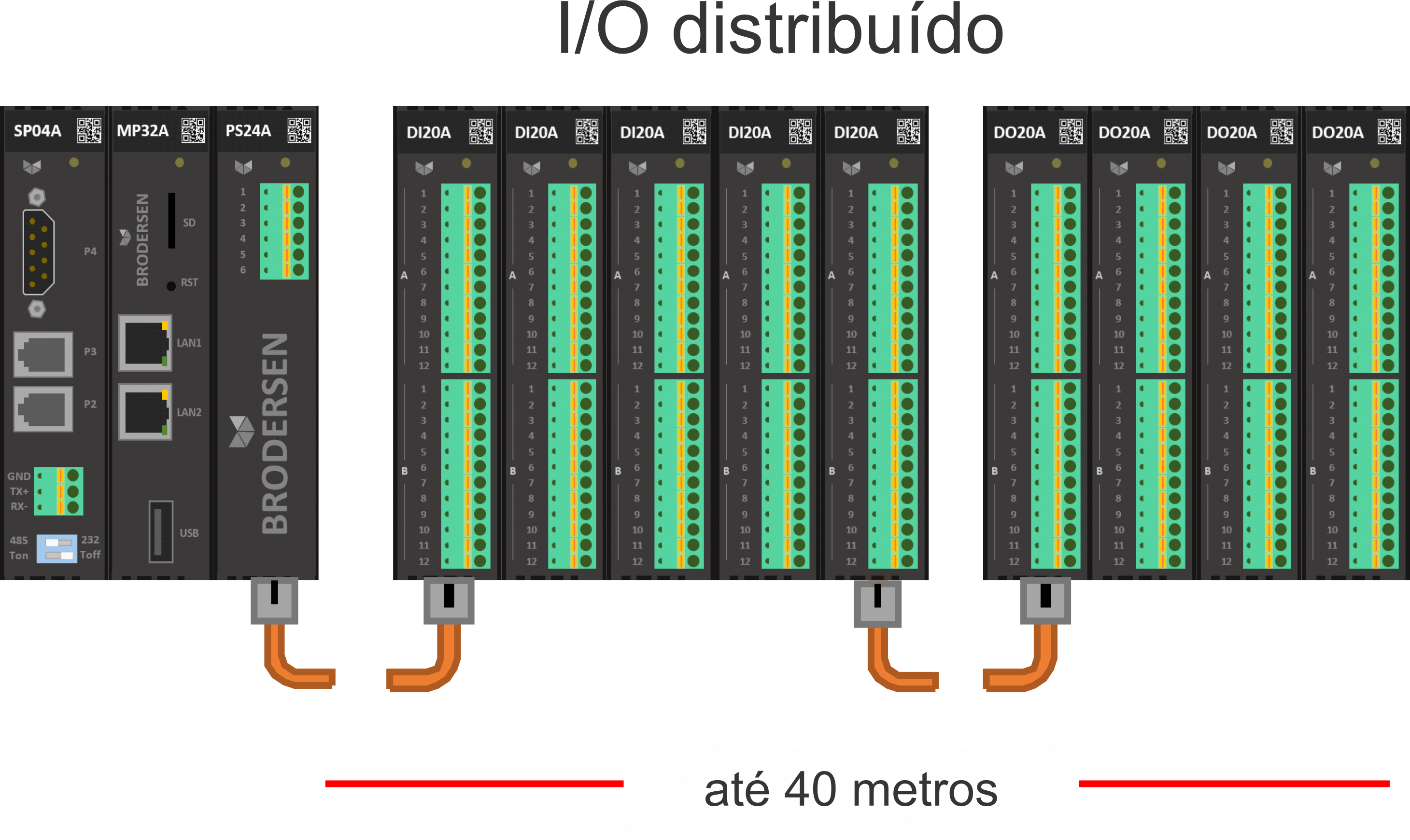
The maximum total length of a complete LB2 system, with local/distributed I/O, is 40 meters, including the interconnecting cables of remote or distributed racks, with each module accounting for 2 cm.
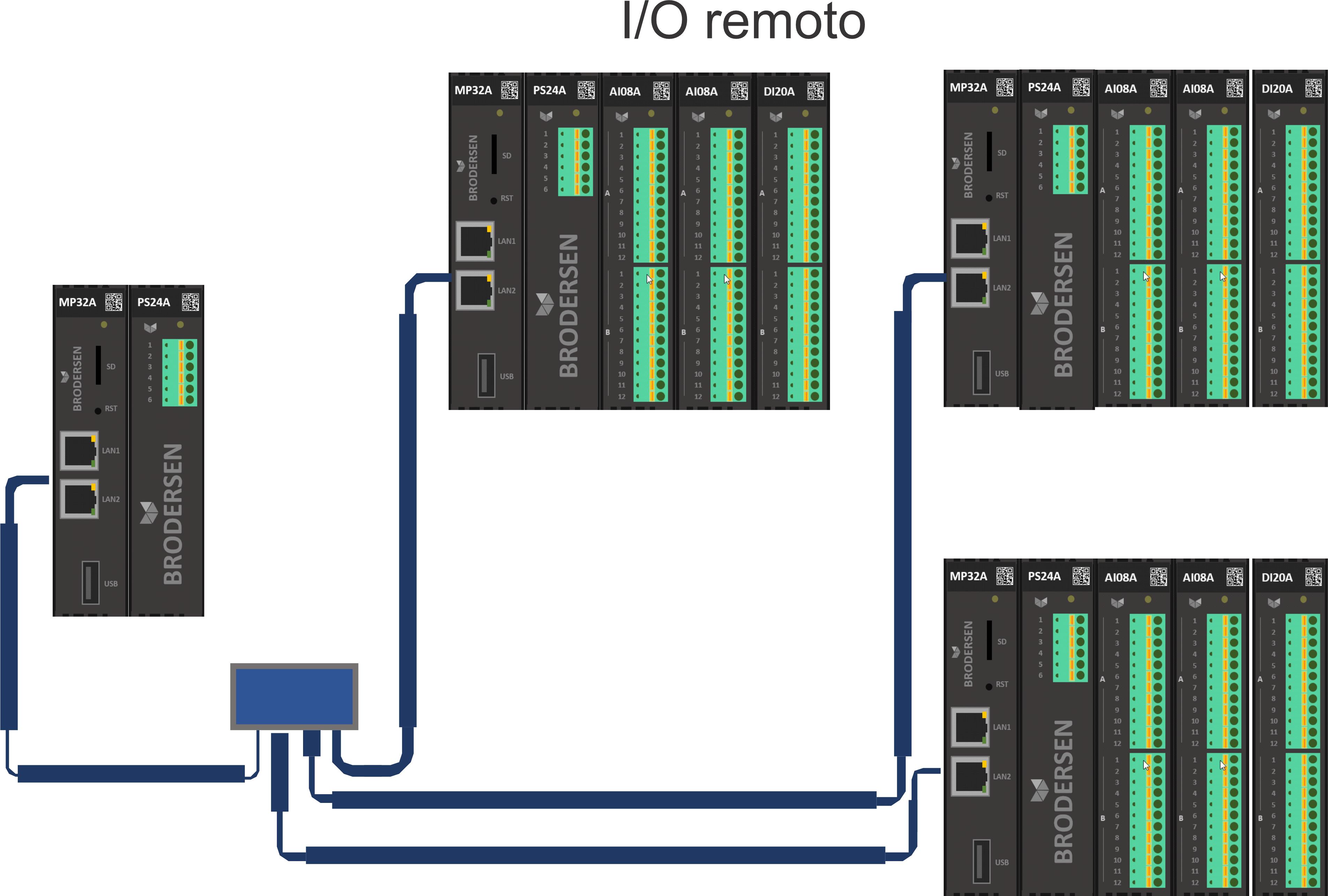
When used for plant automation and/or large systems, Brodersen PLCs/RTUs can utilize topology with remote I/O…
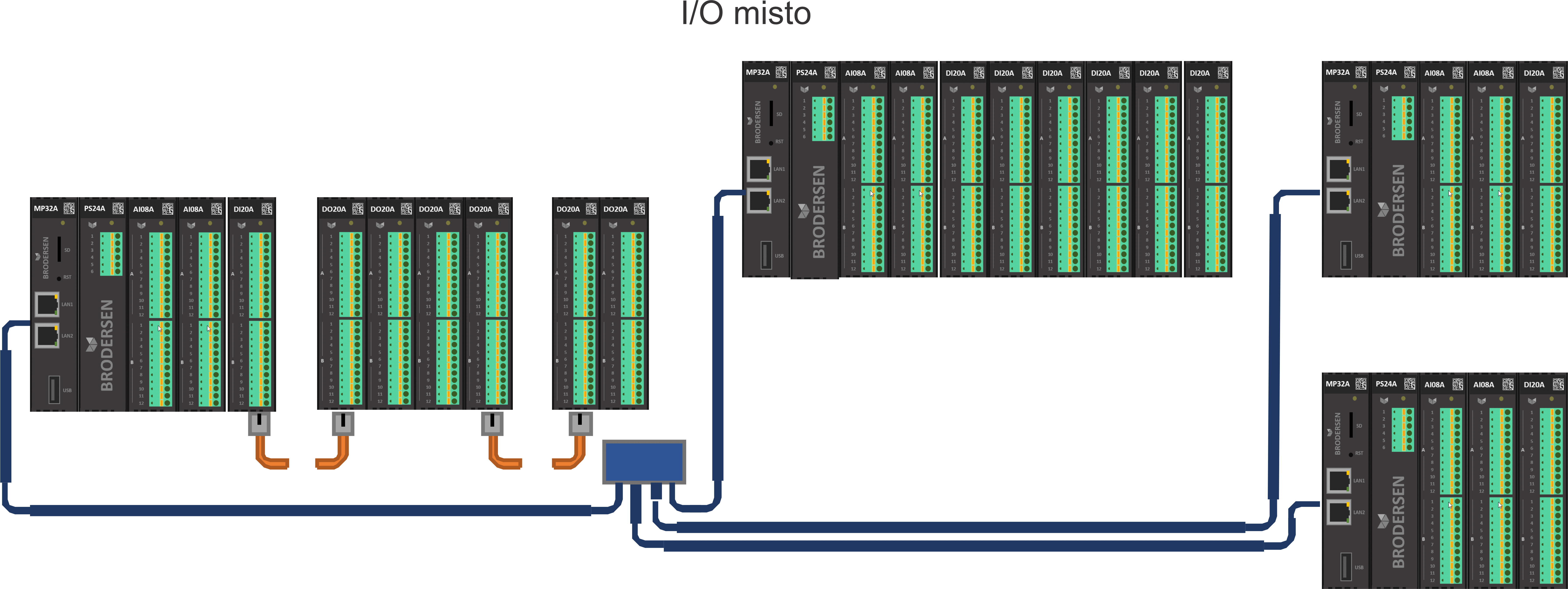
… or even mixed topology, with remote and distributed I/O, including fiber-optic interconnection for systems in large, scattered areas.
The software Worksuite
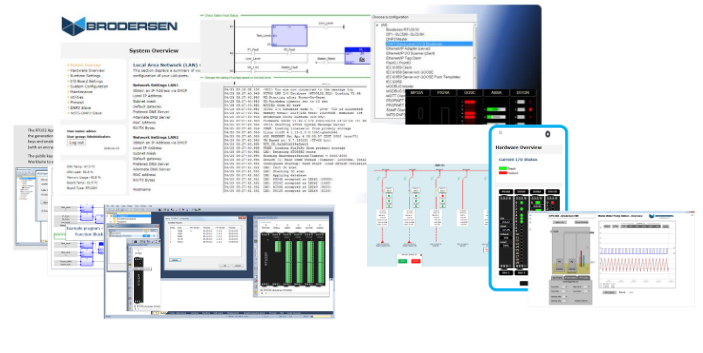
WorkSuite provides a powerful and flexible development and testing platform for the creation of applications for the RTU32M/N RTUs/PLCs, as well as testing and commissioning. The Worksuite platform includes ‘wizards’ and software tools that enable rapid configuration of local and remote I/O, communication interfaces, data storage and transfer, and user interfaces (HMIs), as well as the development of logic programs. The Worksuite platform includes wizards and tools that allow the quick and efficient configuration and parameterization of applications, as well as their interfaces.
Once connected to the PLC/RTU, the list of I/O modules is automatically generated and only the configuration of the installed topology modules needs to be uploaded. If it is not connected, add modules from the menu to create the desired layout, and when connected, do the reverse path, i.e., download the desired topology.
With a large number of communication protocols, and the possibility of creating custom protocols, each system tag can be used by several protocols simultaneously, which makes Brodersen PLCs/RTUs a robust and reliable protocol gateway.
The user is free to choose to program in Ladder, function block diagram, structured text, or other languages standardized by the IEC 61131-3. It is possible to simultaneously use more than one language within the same application and also convert a program between them at any time.
With local, network, or modem access, the Worksuite platform complements the RTU32M/N, not only in process control applications, but also in RTU applications, whether local or remote.