zenon platform in PHARMA industry
Leave your details and we will contact you
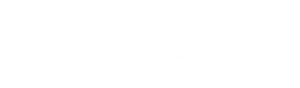
The pharmaceutical industry manufactures a wide range of essential products, which has made companies in this sector highly profitable. At the same time, pharmaceutical manufacturers face unique challenges. As one of the most heavily regulated industries, the pharmaceutical industry must continuously monitor its compliance with local and international regulations and standards. Failure to comply with regulations can lead to unsafe products, costly fines, delays in product approval, and even criminal charges.
The need to comply with regulations means that every step of the pharmaceutical manufacturing process must be traceable and thoroughly documented. In the supply chain, for example, pharmaceutical manufacturers require end-to-end transparency.
The high level of risk present in the pharmaceutical industry has made many manufacturers hesitant to move away from paper documentation and embrace full factory digitization. As drug patents expire, however, production efficiency becomes increasingly important. At COPA-DATA, we have developed our zenon pharmaceutical manufacturing software to help companies overcome industry challenges and optimize their processes using innovative technology.
The benefits of zenon for the pharmaceutical industry
zenon is a software platform designed to help pharmaceutical manufacturers automate their manufacturing facilities and manage data more effectively. Consisting of two main elements, engineering environment for design creation and operational application, the zenon platform simplifies the control and execution of your production line. In addition to features for project design and implementation, the software encompasses HMI, SCADA, reports, alarms, and more. This comprehensive design means that zenon improves many aspects of production right from the start of your deployment. With its models and functionalities, zenon offers the ideal HMI for pharmaceutical industry operations. However, even though it is quite comprehensive, the zenon Software Platform delivers efficiency in pharmaceutical production, from large-scale production to small quantities.
Compliant with industry regulations
Digitized systems implemented by pharmaceutical manufacturers must comply with all applicable local and international regulations. To minimize the effort required to achieve compliance, zenon meets FDA 21 CFR Part 11 and Annex 11 of the EU GMP guidelines as standard. Both regulations deal with the proper use of electronic records and computerized systems. As a configurable software, zenon also meets the GAMP 5 Software Category 4 requirements.
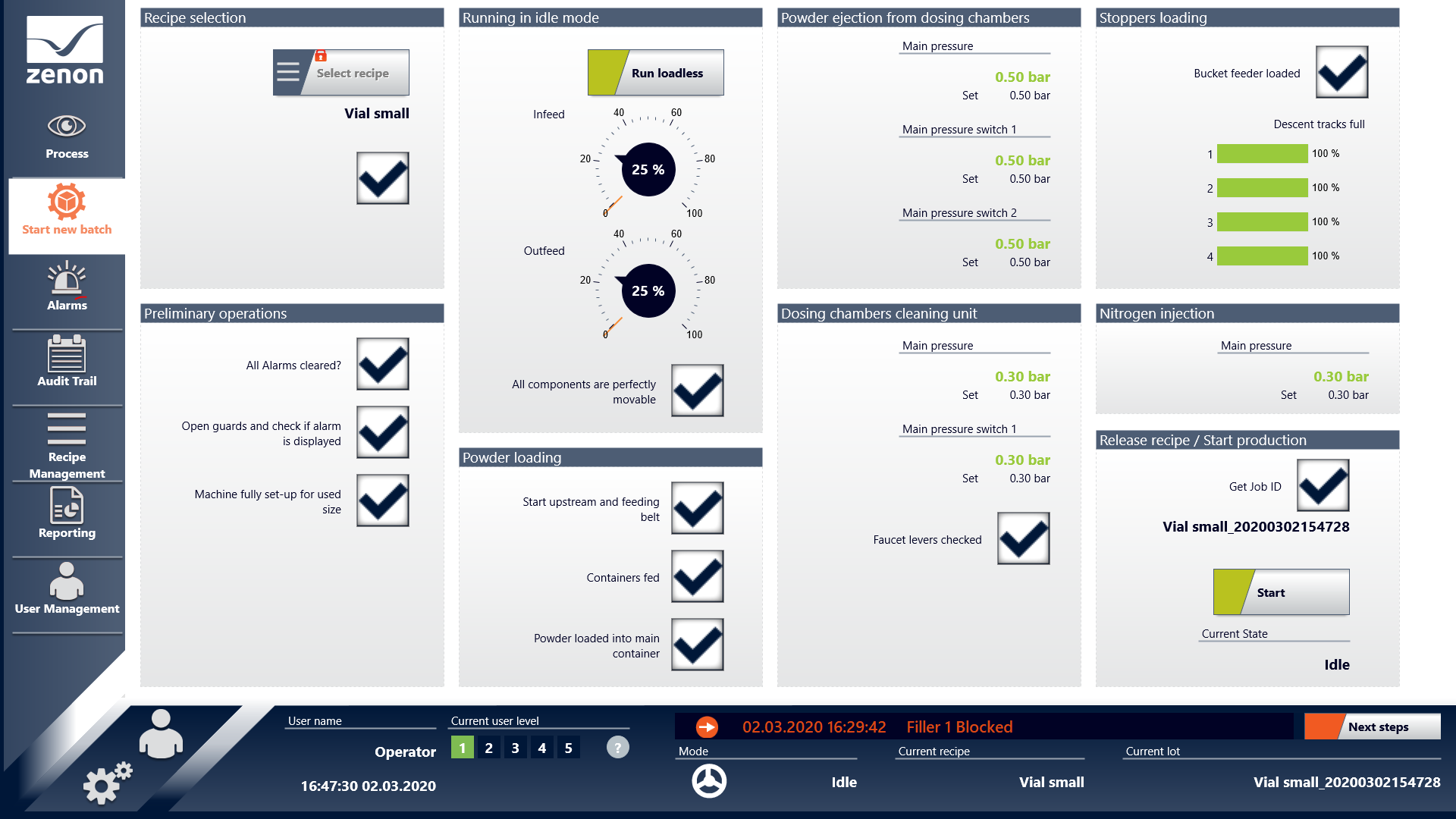
Flexibility ensures quality in production
With zenon’s Batch Control and Recipe Management, ISA88-compliant production is characterized by a high level of ease of use and flexibility. Reporting and documentation are completely automated in zenon. As a result, quality assurance and production can be seamlessly combined, as quality reporting and analysis are available at the touch of a button.
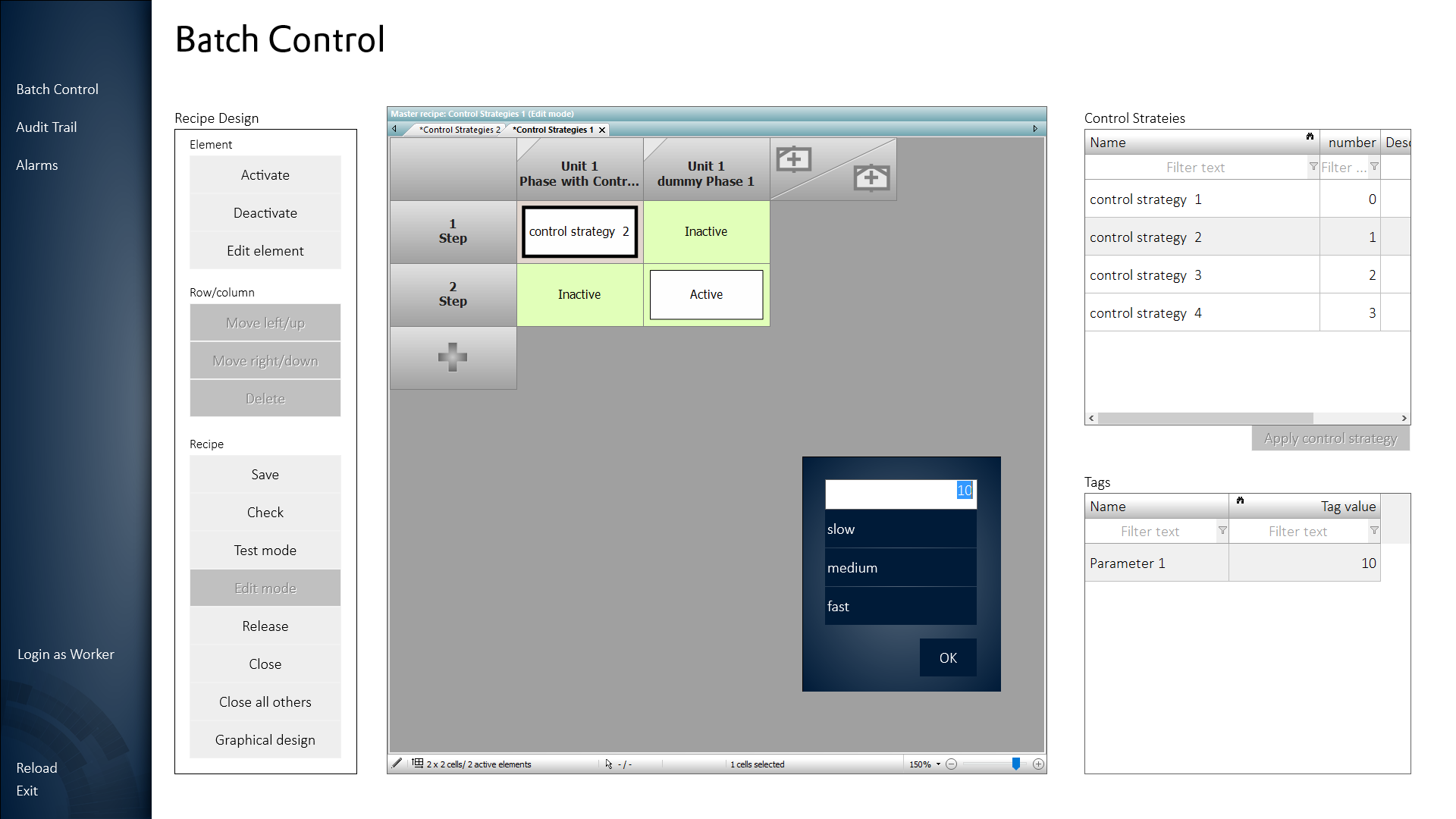
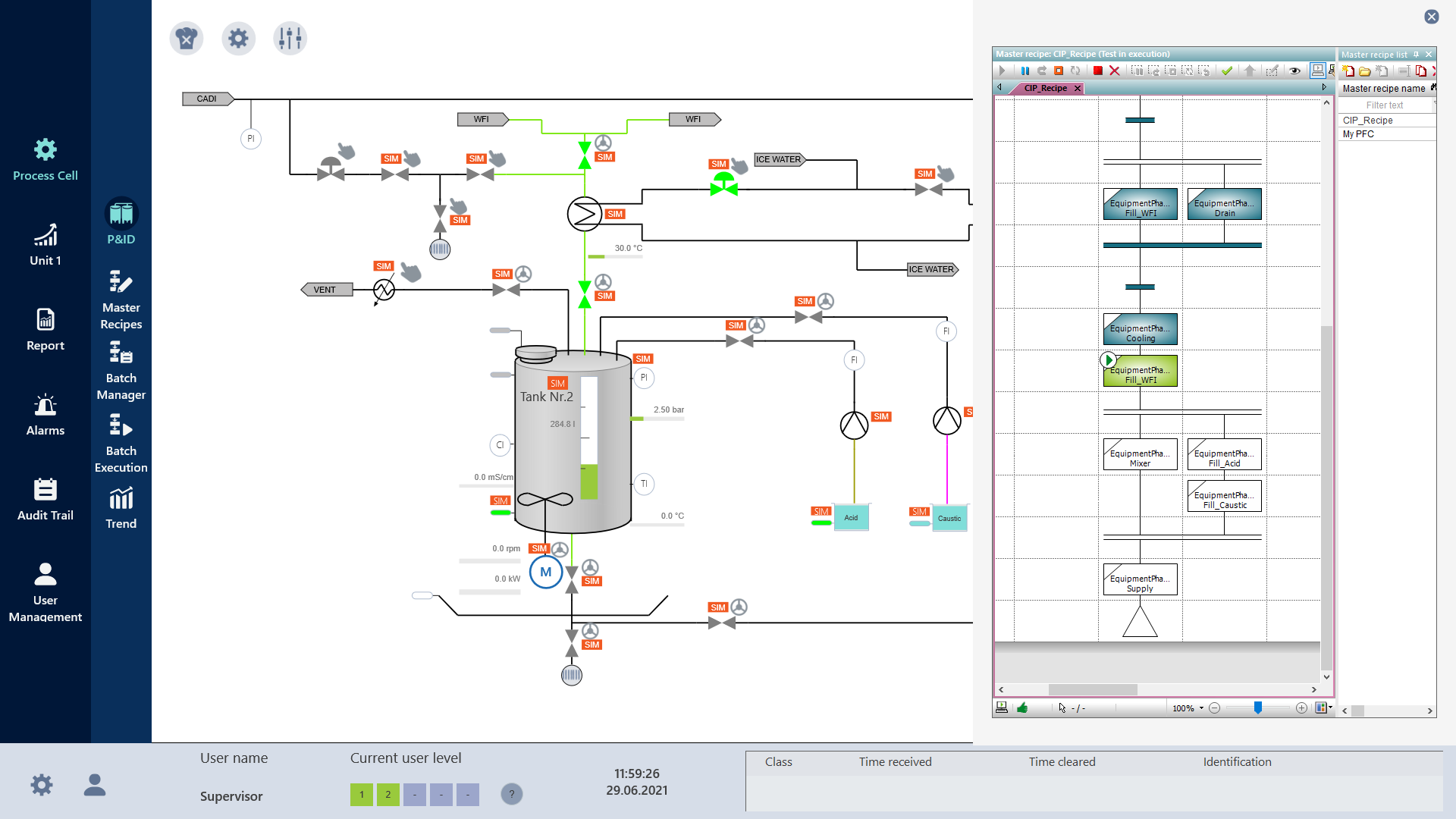
Reduced validation work
The efficiency of engineering tasks at zenon together with reduced validation work bring a greater potential for innovation to the pharmaceutical industry. GMP designs and FDA 21 CFR Part 11 compliant designs can be created in the blink of an eye, since zenon is classified as a configurable software according to GAMP 5 Software Category 4. Therefore, the project is already created validated in these standards, as well as any maintenance or expansion of future production of the production.
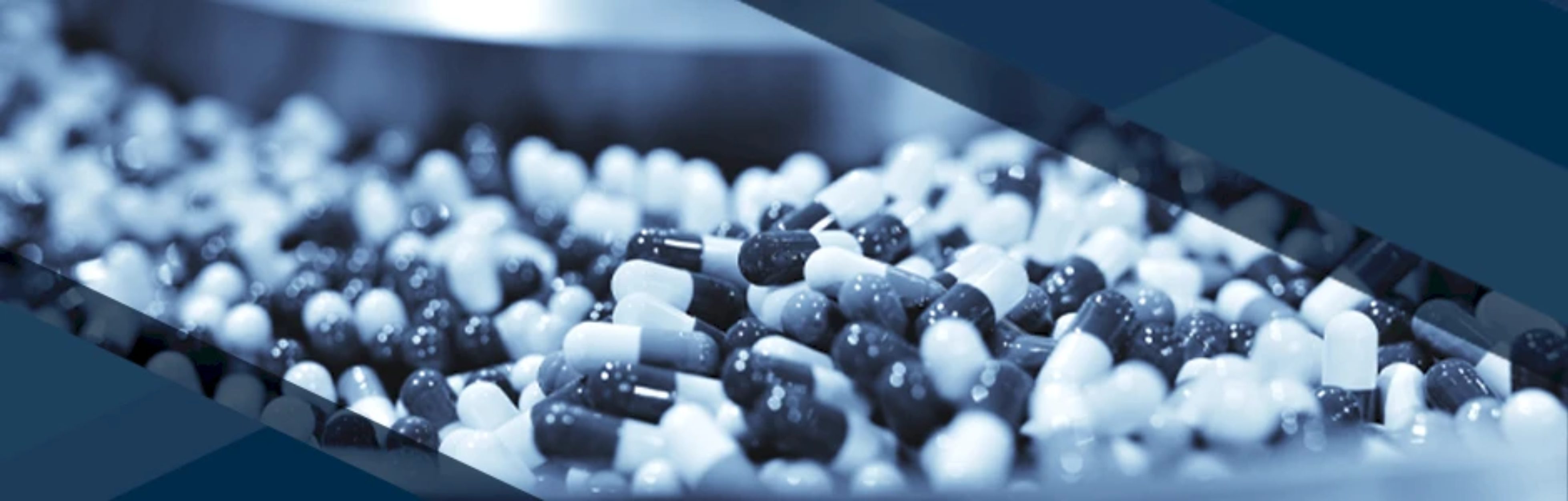
Efficient and reliable data storage
The zenon platform eliminates the need for paper-based documentation during production, reducing the likelihood of error and making data available immediately, whenever it’s needed. To ensure traceability of changes and deletions, zenon records data with an attached timestamp. The software stores data centrally, which means you’ll still be able to access it if the device you use to save it is, for example, lost or damaged. A more secure archive means reduced risk for your business.
With zenon, you can create a fully functional runtime system without adding additional servers. By providing everything you need to optimize operations in a single package, pharmaceutical manufacturing software keeps your overall cost of ownership low.
Reducing manufacturing costs means evaluating your processes, identifying inefficiencies, and making targeted changes. The zenon platform gives you easy access to the data you need to make these assessments, introduce changes, and reduce the financial risk related to non-compliance.
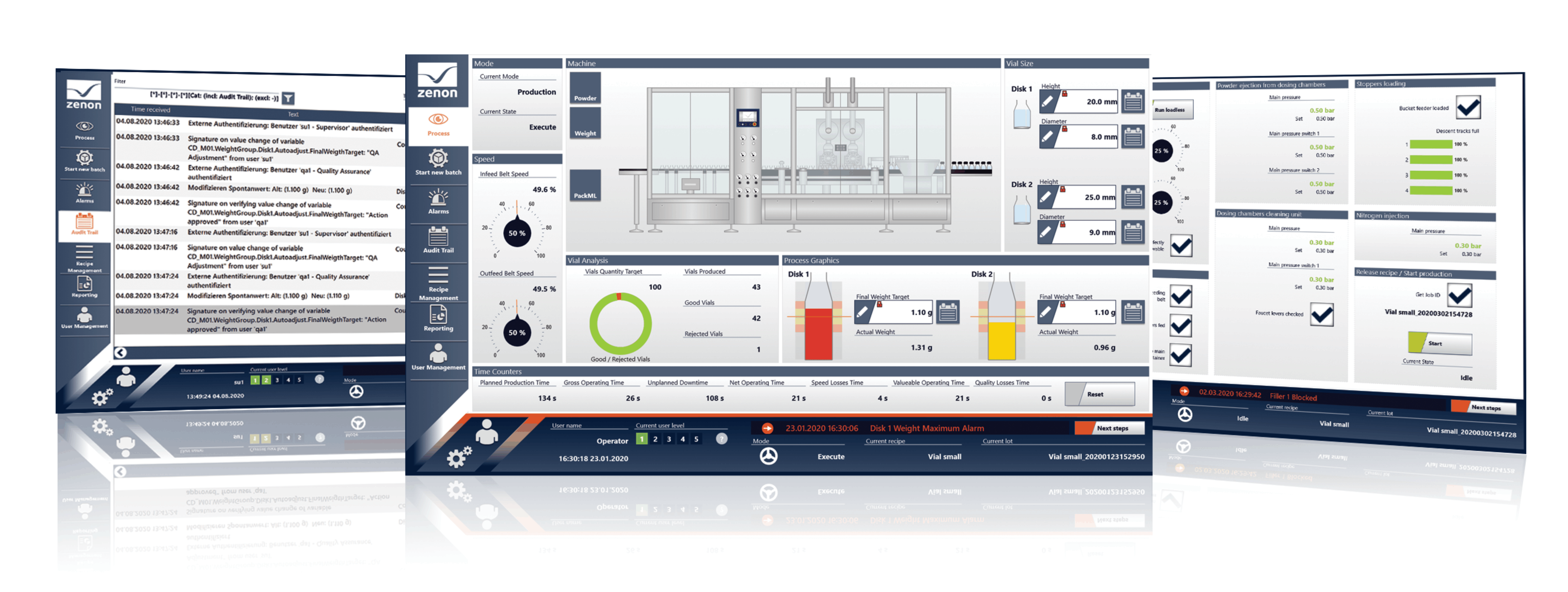
Improve pharmaceutical operations and management
For the pharmaceutical industry, zenon enables manufacturers to retire obsolete processes, streamline operations, and comply with regulations that are actually intended to ensure product safety, quality, and uniformity. COPA-DATA, the company that develops the zenon platform, has more than 30 years of experience in the development of industrial automation solutions for demanding sectors, which guarantees the confidence of users, both for the automation needs of the present and for what will come in the future.
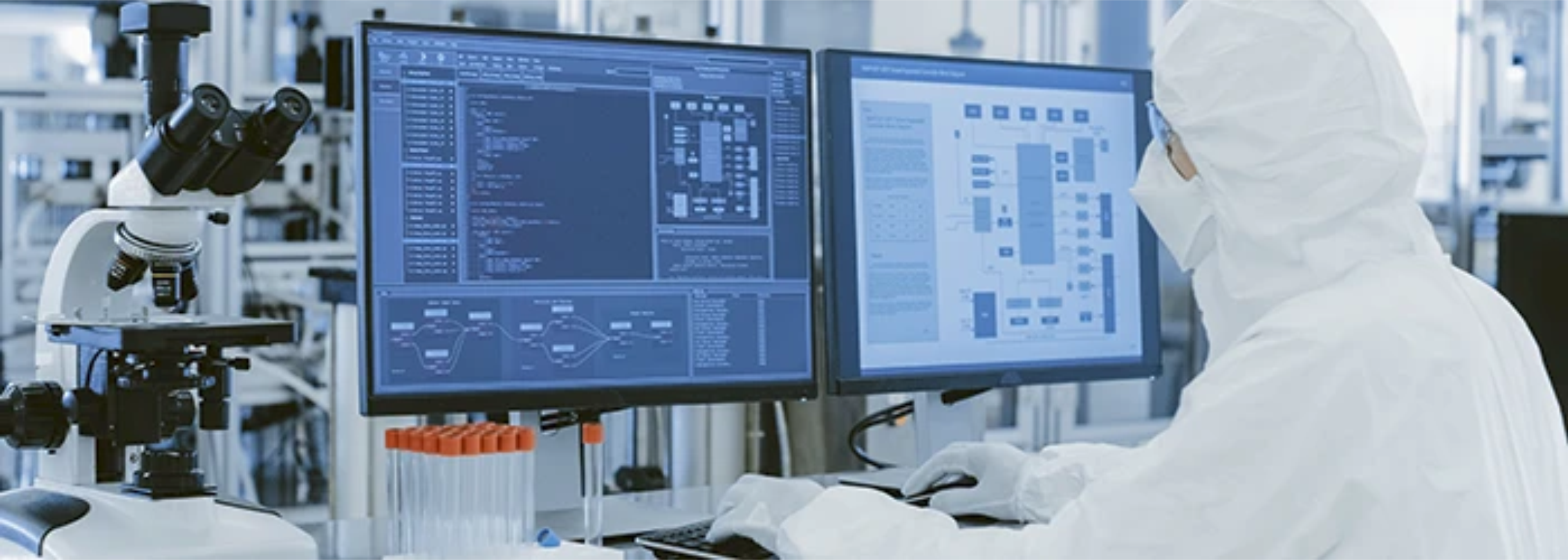
Pharmaceutical companies are under pressure to make production lines and their processes increasingly flexible and compliant with data integrity regulations. To meet these requirements, a Manufacturing Execution System (MES) and Industrial Control Software are required, not only in terms of functionality but also in terms of usability. However, most businesses still rely on error-prone manual documentation. Thus, bridging the gap between your MES and your Industrial Control Software becomes even more challenging.
Needless to say, the transition from paper-based batch records to electronic records is one of the biggest aspects of the pharmaceutical industry.
The challenges and limits of the Classical Approach
In the current approach, MES is used to exchange messages with a unit, including all parameters such as batch ID, product name, and recipe name, while most automation software uses real-time values.
MES systems, like all IT systems, are not designed to exchange real-time values with SCADA and PLC. Communication between the MES and the shop floor takes place in a transactional way, through the exchange of messages at the specific moment.
This means that converting between the two is not easy and can create limitations with data integrity. Production results and any exceptions (e.g. a critical product quality alarm) are not transferred to the MES system. Therefore, operations need a simplified integration of MES with their Industrial Control Software to benefit from the flexibility that the industry requires.
The right industrial control software will help your factory with daily challenges
This is where a communication interface called MSI (Message-based Shopfloor Integration) comes into play to address the limitations of current OT and IT integrations.
Today, WERUM PAS|X is the primary Pharmaceutical and Biotechnology MES used to implement Electronic Batch Records (EBR). To communicate with shop floor equipment, PAS|X offers the MSI interface which is designed as a message-based solution and is based on standard OPC-UA communication technology and REST-based web services. PAS|X sends batch parameters in messages to the Industrial Control Systems and receives GMP values or exceptions.
Using zenon as an Industrial Control System you will be able to fill the gap with Werum PAS| X offering a built-in configurable MSI interface to connect machines and manufacturing lines with ease.
Does Werum PAS/X integrate with zenon?
zenon’s MSI interface allows you to receive and send batch information to/from PAS|X directly to your equipment, as well as sending GMP alarm data. The integration of zenon with Werum PAS|X will allow you to reduce errors, improve batch release time, and reduce downtime between batches. But most importantly, it allows you the flexibility you need in a modern pharmaceutical facility.
The current version, with its innovative functionalities, guarantees an unsurpassed level of usability by supporting the following MSI messages:
- Order parameter message: used by PAS|X to send parameters to zenon, or by zenon, to send back counters and values. (e.g., Initial Batch, In-Process Controls, End of Batch).
- Exception message: Triggered by zenon when a relevant GMP deviation occurs during batch execution. (e.g., when the Sterilization Low Temperature Threshold Alarm is enabled).
- Order status message: triggered by zenon to inform PAS|X about the current state of the equipment or operation in progress. (e.g. “Download recipes for PLC in progress…”).
- Message to abort the order: Triggered by zenon to inform PAS|X to indicate that the order or prescription on the machine has been aborted.
Some of our clients
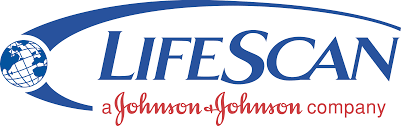
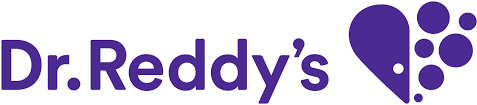
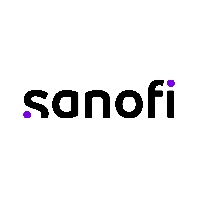
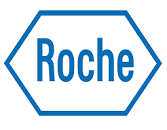
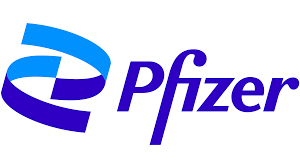

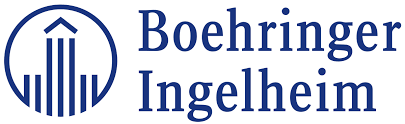
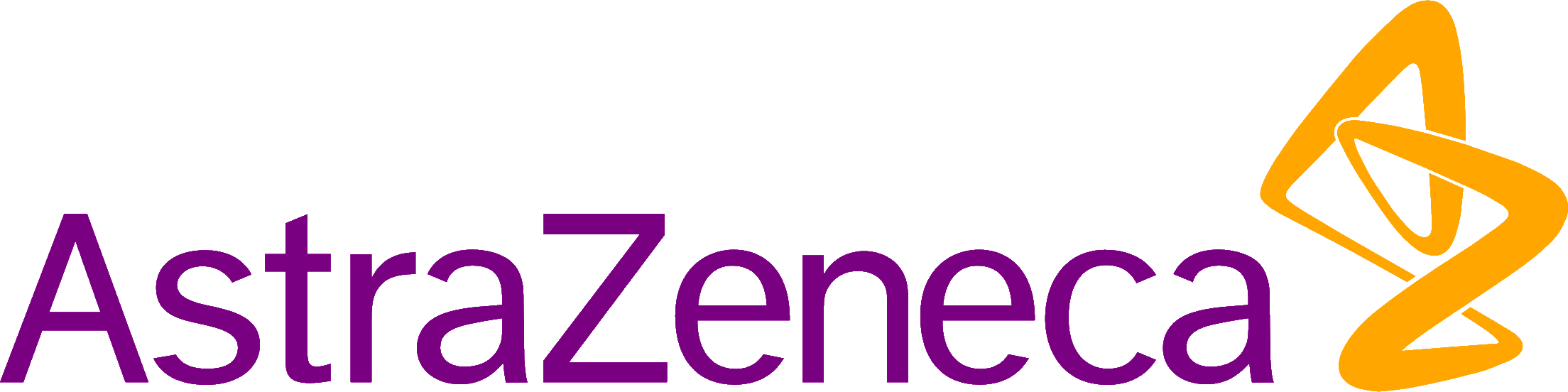

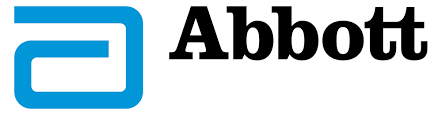